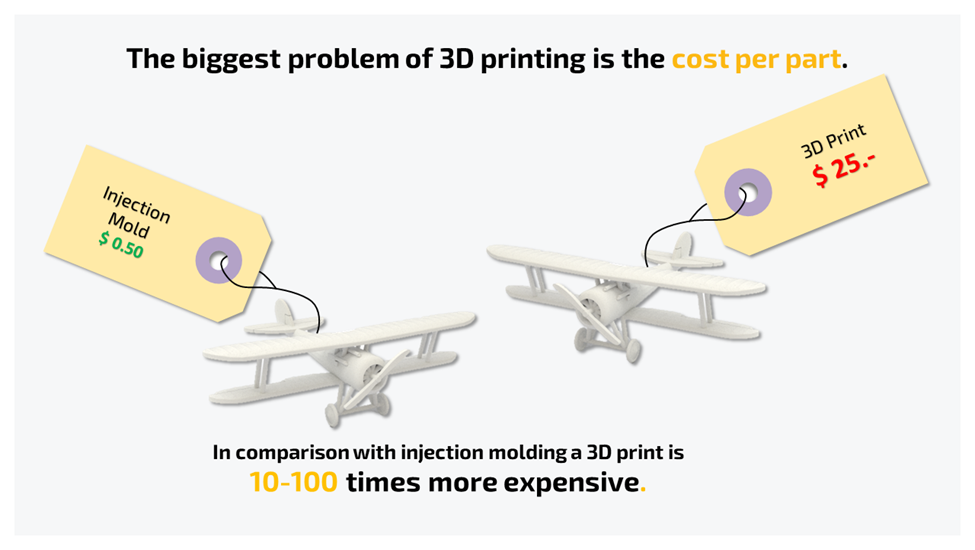
So, what is holding additive manufacturing back from broad industrial adoption and scalability?
As with most things in the industry, a lot of it comes down to cost. Today, the cost of 3D printing parts is still too high to be truly viable for many applications. To give an idea, the price of 3D printing is still between 10 to 100 times more expensive than injection moulding. This reality has limited additive manufacturing to niche, high-value applications, where the cost per part is outweighed by the performance benefits or is balanced by small production volumes. It goes without saying that by lowering the price per part, AM adoption and scalability will accelerate.
Before looking at how to drive the cost per part of the AM process down, it is first important to understand what is at the root of the elevated cost ratio in the first place. Three key factors influence the cost of 3D printing parts: the depreciation of the 3D printing hardware, the cost of raw materials, and the price of labour.
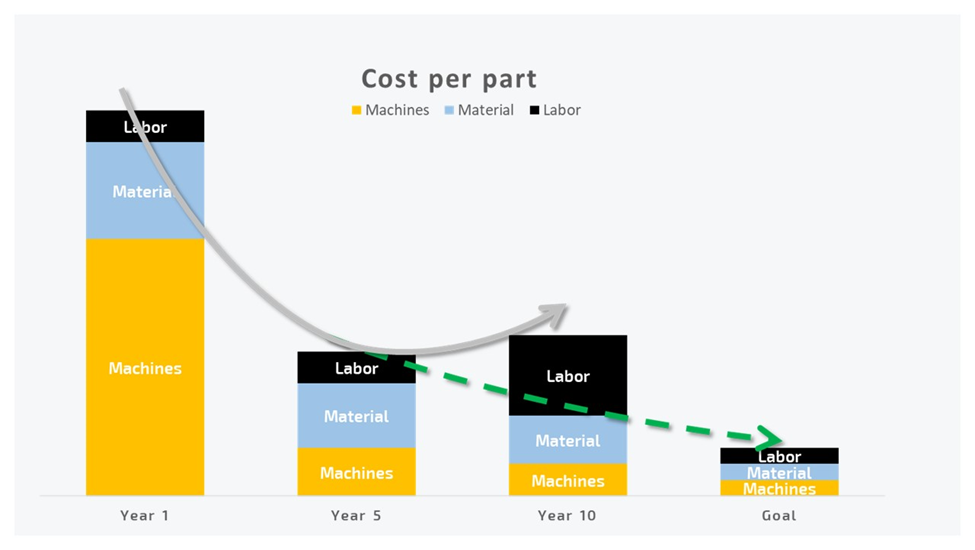
The first two cost drivers can be addressed easily enough. 3D printer depreciation refers to the value a hardware system loses over time due to usage and position in the market as new machines are released. This cost factor can be mitigated by gradually writing off AM equipment. As for raw materials, the cost of 3D printing consumables will decrease as greater volumes are produced and purchased. The increased scalability of AM will therefore naturally drive the cost of materials down.
It is therefore vital that all process efficiency losses associated with industrial 3D printing be minimized. In doing so, costs will not increase exponentially with expanding production, which will pave the way for AM factories to scale their operations while maintaining competitive price levels. A lower cost per part will also create pathways for new businesses and industries to invest in and adopt AM.
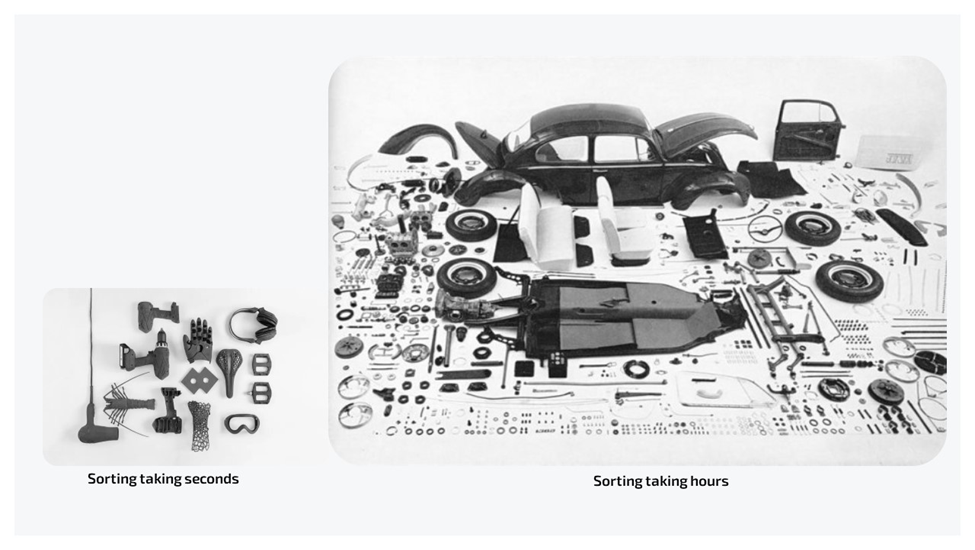
Fortunately, advances are being made to enhance the automation of the additive manufacturing process. AM-Flow is tackling cost per part in AM by zeroing in on one of the most costly steps in the 3D printing process chain: post-production. The company offers a full-stack solution, combining cutting-edge technologies like computer vision, machine learning, and smart robotics to achieve an end-to-end automated post-production workflow.
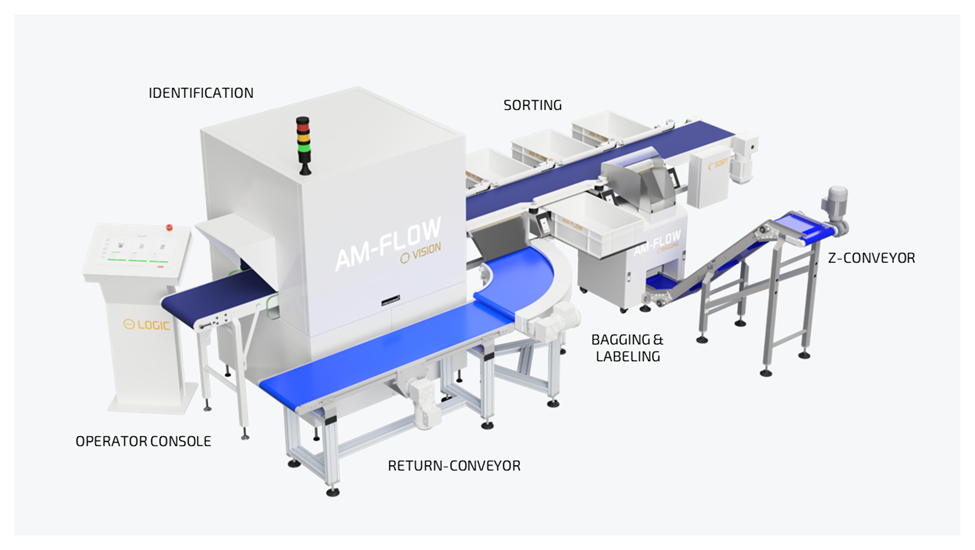
AM-Flow’s multimodule solution is centred on the AM-VISION, a sophisticated system that uses computer vision to identify and sort parts based on their geometries—each in under a second. This system is supported by a selection of other modules, including AM-SORT, a customized high-speed sorting station; AM-BAGGING, a bag and label unit that prepares parts for shipment; AM-PICK, a robotic bin picking system designed to move from a batch to one-piece flow process and back; and AM-ROUTE, an autonomous mobile robot that transports parts from station to station. All these modules are seamlessly connected by AM-LOGIC, the operating system that integrates all of AM-Flow’s modules with the user’s existing IT infrastructure.
Automating post-production is the next step in scaling additive manufacturing. Automating will significantly drive down the cost per 3D printed part, even as production output increases. Cost per part will be the flywheel of growth in the AM-Industry; that’s the relevance of cost per part for our industry.
The issue I have with this paragraph is that it can be interpreted as that our solution will cost jobs. The story line needs to be built around process efficiencies required to be able to scale the industry; it should be less about people, labour and thus, jobs. What we will impact is that one does not need to recruit to deal with the consequences of scaling production.