Established in 2018, AM-Flow is now a leader in automating additive manufacturing (the industrial face of 3D printing). “Our mission,” says Stefan Rink, CEO at AM-Flow “is providing the global AM Industry with cutting edge Industry 4.0 technology. Creating end-to-end digitized AM (3D Printing) production processes, and supporting to achieve the full potential of additive manufacturing – from democratization of design to sustainable manufacturing.”
Answering unique challenges
For manufacturers who are running industrial 3D printers, the world of high-mix, high volume products presents unique challenges. Normally, when you start automating a factory process, the first step is standardizing the product portfolio. In additive manufacturing, variation is the name of the game. E.g. infinite varieties of geometries and materials are currently being printed in large volumes on daily basis. “When you have a factory producing multiples of a wide range of parts or 3D-printed objects out of the same printer, they must be unpacked, cleaned, identified, sorted, tumbled and usually dyed before bagging and shipment,” explains Carlos Zwikker, CCO at AM-Flow. “That’s a lot of processes, covering a lot of production space, and requiring even more manual labour.” To this end, AM-Flow has clear objectives wrapped around well-defined system solutions.
Refreshing approach to business
AM-Flow has a logical approach to automation, with modular solutions available for each stage of the additive manufacturing process. Automated identification, machine vision based on the part’s geometry only, sorting, picking, bagging, labelling, and transportation each are separate modules that customers can choose from. They have a refreshing way to do business too, with a smart business model that’s helping customers take the first step.
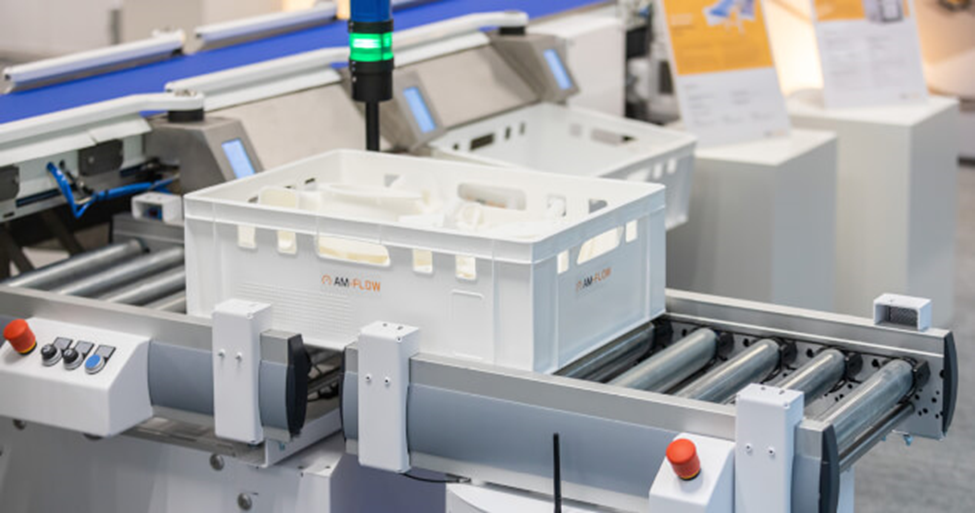
“Customers who aren’t quite sure about committing to a full upfront investment are welcome to take on our solutions on a pay-per-use basis,” says Carlos Zwikker. That means minimum investment upfront, with all the benefits of AM-PICK, AM-VISION, AM-SORT, AM-BAGGING, and AM-ROUTE available under a ‘pay-as-you-grow’ arrangement.
Smart AM Factory
As those customers grow, their business expands, and their needs for specific production and workflow information increases, which is where the AM-EXPERT service comes into play. “We work with customers to analyse their existing workflow and seek potential for improvement,” Carlos says, “helping them develop their business case, looking to areas that can benefit most from automation. Our end customers are already designing around the clock globally and the 3D printers are running 24/7.” The last step to get to a smart factory is to automate the remaining manual process steps between the printers, and the distribution centre. This will substantially reduce the cost per part and drive further adoption of AM.
Human robot collaboration
For businesses that expand in size, as well as those with processes already spread across the production floor, AM-ROUTE is the go-to solution for internal transportation. Thanks to support from OMRON, one task in particular no longer requires the same level of human interaction: in-house transportation, routing goods from point to point within the facility. “The job of moving supplies of (semi-) completed goods from one production process to the next, or to the distribution centre, is now automated. With help from OMRON, we offer a fully autonomous mobile robot (AMR), the AM-ROUTE,” says Stefan Rink
Closed loop tracking & tracing
For Ronald Mol Regional Account Manager at OMRON in the Netherlands, the partnership is a perfect match. “We are delighted to work with AM-Flow in providing their customers with the benefits of our LD-60 Autonomous Mobile Robot (AMR). This unit from the LD-series has a payload of 60 kg, natural feature navigation and easy deployment in an industrial setting – no modifications are required to the facility.” The LD-60 is an autonomous robot, with self-mapping and self-navigating operation, automatically planning its route to prevent collisions, using a safety scanning laser and low front laser for obstacle sensing. Connected to the factory system using Wi-Fi, it can be programmed to shuttle between stations (at 1.8m/s) collecting and delivering pieces, with full traceability of all pieces at every stage.
Autonomous Intelligence
“This is an intelligent vehicle at work within an intelligent system,” says Ronald, “working to maximize machine uptime by reducing idle time, and eliminating human error. The whole portfolio of services and solutions offered by AM-Flow are perfectly in sync with the growing shift to automation, and OMRON’s AMRs are a proud part of that offer. We will continue to support AM-Flow and their customers, indeed any business who wants to benefit from the transformative power of Industry 4.0.”
For more information about this article please contact OMRON or AM-Flow.