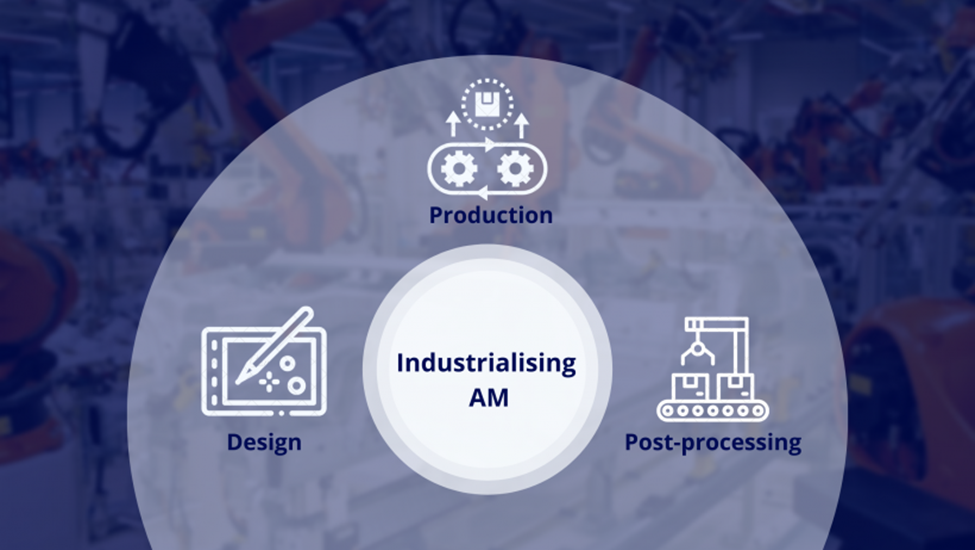
Automating design for additive manufacturing
A significant part of designing for additive manufacturing (DfAM) remains manual. Even a skilled engineer can spend from 30 minutes to a few hours on a new part understanding the best orientation, technology and material.
For manufacturers looking to adopt AM for hundreds of parts, it could cost tens of thousands of dollars in engineering time over a year just to determine whether and how to 3D print each one.
AM software companies are approaching this challenge in several ways to simplify the design stage and advance AM to a scalable technology.
For example, Ntopology’s nTop software offers reusable design workflows, whereas certain repetitive tasks, like creating lattice structure or adding serial numbers, can be automated.
In further efforts to understand the viability of designs, PrintSyst developed an AI-based tool that allows engineers to assess STL files and get insight into suitable processes, appropriate materials, and anticipated cost. A result is a tool that allows engineers to make quick, easy and accurate decisions about 3D printing.
However, for more complex applications, like composite or metal parts, simple file assessment may not be enough.
This is where simulation software comes in, allowing engineers to model the printing process and predict the effects of different parameters on the material properties. This approach saves time and cost associated with trial-and-error build modelling.
That said, simulating the AM build can require significant computational resources, although some software providers aim to overcome this hurdle by connecting their design and engineering tools to the cloud, offloading intense calculations.
But the ultimate development that is opening the door for streamlined DfAM is interoperability and connectivity across different design and simulation tools.
That’s why we’re witnessing more and more partnerships between smaller software companies, while bigger players work on bundling their offerings under one solution. For example, Autodesk has been folding its suite of Netfabb tools for 3D printing into its
Fusion 360 suite and has also recently announced the addition of a simulation extension.
This trend falls into the bigger movement of creating a connected digital thread, where data flows easily across the design, production and post-processing stages. And this brings us to the next exciting development of digitised additive production management.
Digitised AM production management
Industrialising AM means removing as much manual labour as possible to enable efficient, scalable and error-proof production. In this regard, one trend that manufacturers should be aware of is the rise of advanced production management solutions.
In AM, production management covers the key stages of the AM production process, such as bundling orders for a build, scheduling AM systems, planning post-processing and QA operations and tracking that each step is performed as planned.
However, many users of AM technology still rely on their staff to do these tasks manually with the help of poorly fit solutions, like spreadsheets, making data re-input and errors a norm.
Digitising production management processes brings AM one step closer to maturity. It helps to centralise, standardise and automate operations in a way that would never be possible with disparate and manual solutions.
Over the last few years, additive manufacturing execution system (MES) solutions have risen to be the key enabler for this kind of digital transformation.

An example of a use case for additive MES would be the ability to assign incoming orders to printing batches automatically based on specified requirements, like a 3D printer type, its availability and material.
Such automation unlocks many benefits. Since the scheduling workflow is standardised, there is a lesser risk for managers to make mistakes when scheduling AM jobs. Streamlining production workflow in this way helps to scale AM in a flexible manner
Over the last few years, additive MES has also evolved to provide much greater integration with organisational data – including from AM systems – to tie together production, post-processing, supply chain and human resources into a single system.
Having this control over AM operations gives AM manufacturers and managers all the data they need to identify bottlenecks, better utilise resources and make informed decisions to make production more efficient.
Read also: How Can You Transform Production Planning in Additive Manufacturing?
Optimising the post-processing workflow
While 3D printing post-processing technology for polishing, powder and support removal has significantly evolved, one aspect of it has long been overlooked: organising the post-processing workflow to handle high volumes of parts
To understand what I mean, let’s take an average production run with an HP powder bed fusion 3D printer as an example. To maximise the use of the system and material, most manufacturers would try to load the 3D printer with as many parts as possible.
At the end of the production process, these parts – which can often be a mix of different items from different orders – need to be identified, sorted and sent to a relevant post-processing unit.
Currently, these tasks are done manually, which can significantly affect the economics of the entire AM production, especially as it grows. What this means is that when adding a new AM system, you’ll most likely need to hire two or more people to handle the post-processing tasks.
From the bottom-line perspective, it’s clear that this approach is not economically viable in the long term.
To industrialise and scale the use of AM efficiently, the post-production workflow needs to be integrated and automated.
One company pioneering the automation for sorting, tracking and routing of parts post-printing, is AM-Flow. The team at AM-Flow has developed clever solutions that bring us closer to the vision of an automated AM factory.
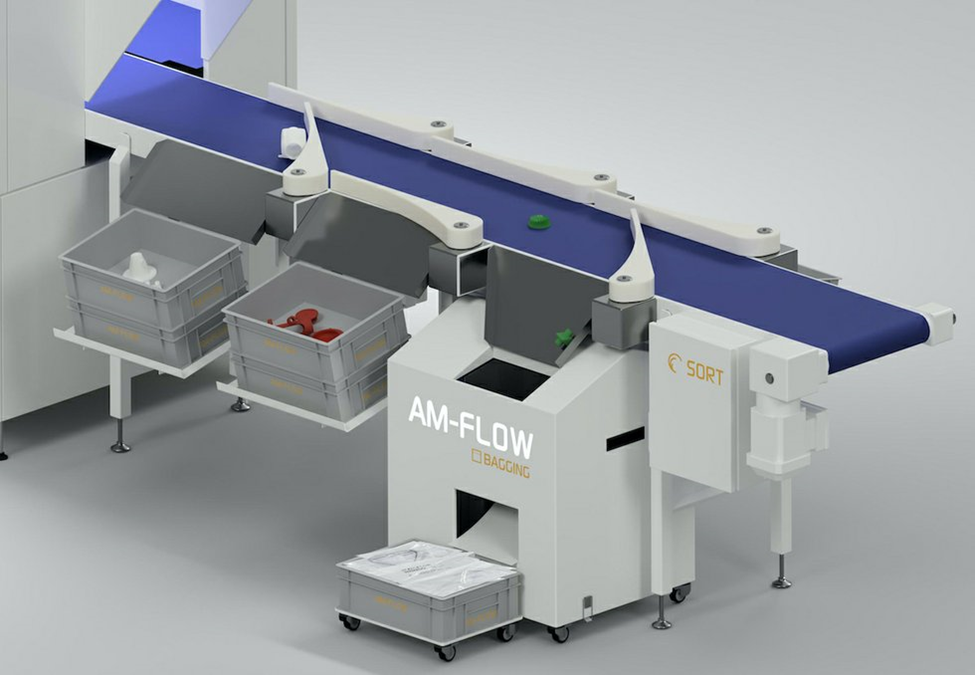
The company’s solution stack includes different modules designed to automate different tasks previously done by staff. For example, one module uses AI-powered computer vision to identify parts after printing, while another is using a robotic arm to move parts to the sorting module, which connects with an automated guided vehicle that delivers the parts to the necessary post-processing stations.
However, to enable the whole process to work in sync, manufacturers need to ensure connectivity between their post-processing operations and MES.
“The logic of how a part moves through a 3D print factory is managed by the MES, the backbone of every digital factory,” says Carlos Zwikker, Commercial Director at AM-Flow in an interview with 3D Printing Media Network.
“We provide the recognition, sorting and routing of the printed parts, where the MES software tells us which printers the parts are coming from and where they need to go next: to post-processing or to be packaged and shipped to the end customer. This way we can provide a full ‘track & trace’ process for AM production lines.”
Industrialising additive manufacturing: The ecosystem approach
As more companies start using industrial 3D printing, it becomes obvious that the cost of AM systems or materials is no longer the key limiting factor to scaling the use of the technology. The AM users face more and more challenges in the ecosystem, where processes are difficult to connect and streamline.
Therefore, the biggest trend driving industrialisation of AM is a common effort within the sector to partner and create solutions to automate and integrate 3D printing processes. Such solutions help AM become a more reliable, profitable technology geared towards reshaping the global manufacturing industry.
If you want to be a part of this trend, start digitising your AM production today
Original article: Industrialising Additive Manufacturing: 3 Key Trends in 2021