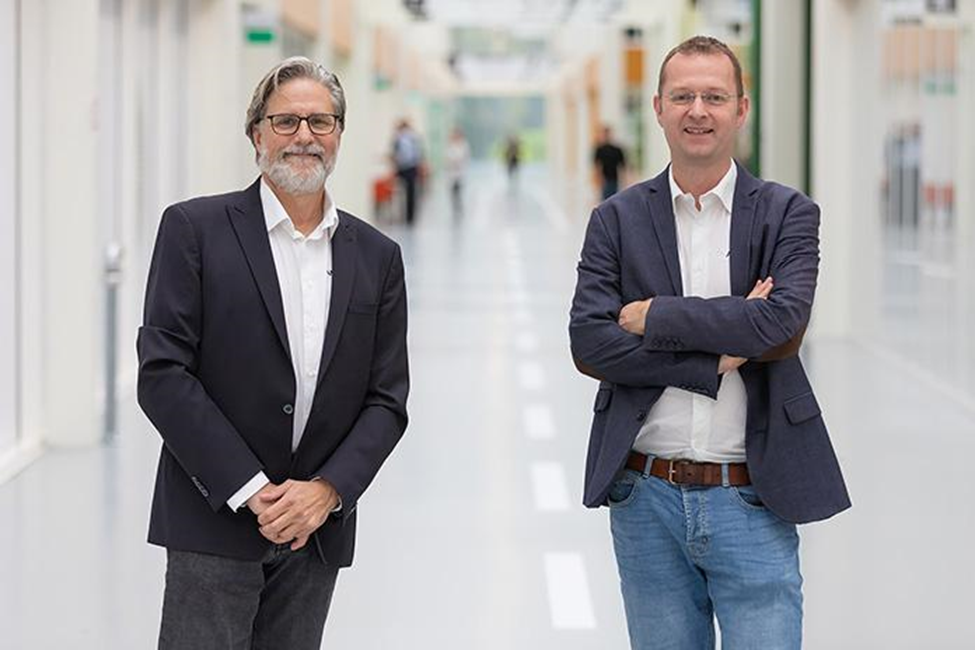
The recent years may have shed light on the advantages of Additive Manufacturing, but companies that are currently disrupting the market, demonstrate the gap between the way operators “traditionally” use this technology and the way the current market requires them to truly take advantage of it.
The undeniable need for smart, on demand and increasingly customized products ultimately implies the use of additional variables that support faster manufacturing and help industries easily shift towards industry 4.0.
What part of these changes are industries missing? We caught up with Stefan Rink and Carlos Zwikker from AM-FLOW to clarify these grey areas.
Together, Stefan Rink and Carlos Zwikker combine over 20 years of experience in Additive Manufacturing. Rink is the CEO and founder of AM-FLOW and Zwikker joined the company almost two years ago as Chief Commercial Officer.
Prior to the creation of AM-FLOW, Rink and Zwikker’s efforts to push activities of well-established 3D printing companies such as Shapeways, make them realize manufacturers initially only focused on the 3D printers:
“What we are seeing right now in the industry is that there is a lot of focus on 3D printing itself and not really in the overall manufacturing process. Additive Manufacturing is a great technology but it is not limited to the printing itself, especially if you want to achieve a full production cycle. Our focus is to enable the shift towards the full production cycle”, the CEO said from the outset.
“It’s been several years that the industry has been talking about Additive Manufacturing and its advantages but it is not possible to truly benefit from the advantages the technology offers if we only lay emphasis on the printing technology. Over time, people find out that printing alone is not going to be a business and this makes the game more interesting because this is not about the printing technology, it’s about manufacturing. At AM-FLOW, we have understood that. That’s why whatever happens after the printer is our focus”, the CCO completes.
From parts identification based on geometry to their sorting for the next process stage
AM-FLOW is a software and hardware company that is on a mission to help any company reach a full Industry 4.0 manufacturing system through end-to-end automated 3D printing processes.
While the hardware technology of AM continues to increase, software companies found themselves addressing a number of issues to support the shift from prototyping to production quality parts. Those issues are observed at the manufacturing level and at the socio-economic level.
Addressing the issue of parts identification at the manufacturing level
For most 3D production workflows, the route towards the 3D printer is sometimes more clear than the one that follows the printing process.
Parts identification, therefore, becomes a key issue for companies that attempt to achieve high volume and high mix production. As Rink rhetorically asked: “if you use SLS 3D printing and you end up with 1 000 parts. How do you manage to identify these parts?”
One approach to solving this issue involves the use of Artificial Intelligence (AI) and machine-learning methods that can automate the process and help operators identify the parts in 0.2 seconds.
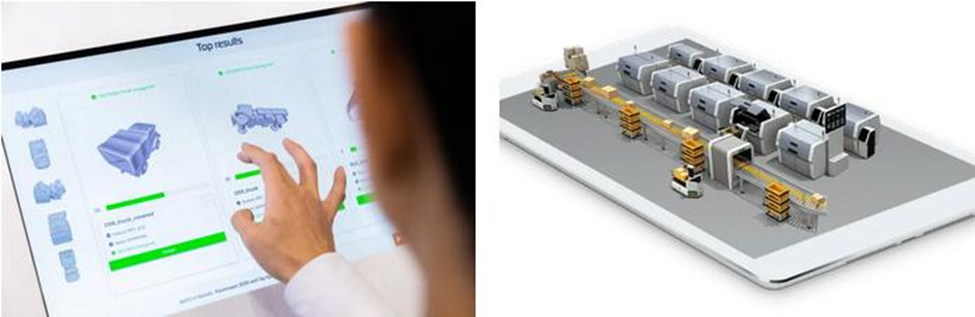
“From the moment operators send their files to the printer, there is no digital information about the part that is being manufactured when it comes out of the printer. We have developed a software that provides tracking & tracing into the AM system,” Zwikker points out.
“Furthermore, 80% of what’s printed before was SLS but metal AM has grown and a lot more is happening today. How do you follow this?
We have made a key focus on developing technologies that can collect data from the very beginning of the process and identify these parts in order to organize their post-processing treatment after manufacturing.
Almost each technology has batch processes and it’s essential to know what part you are printing, what quality enhancing post process treatment is necessary and then bring everything back together to bag and label for shipment”, Rink notes.
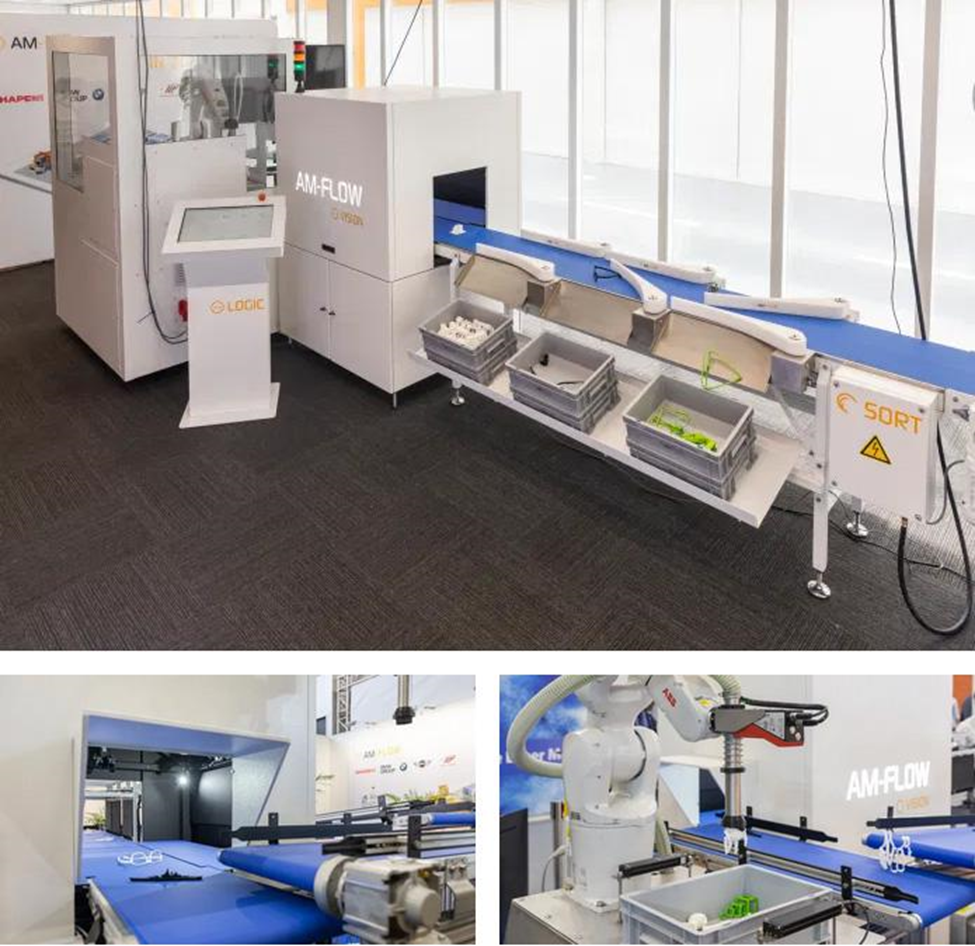
Companies are facing so many pain points to upscale their additive manufacturing production and AM-FLOW is willing to address two of them:
“At the beginning of the manufacturing process, operators should be able to cope with the infinity of geometry that comes out of the printer. At the end of the process, they should be able to achieve post-processing of parts at a high manufacturing speed. These two combined make it complex to upscale a production workflow.
These simple steps are all automated in other incumbent manufacturing environments. But in AM, we are not yet there. Today, less than 10% of parts are actually additive manufactured. The price per part certainly has its part to play, but our aim is to raise this percentage by 20%”, Rink adds.
The key to achieve this automated process is geometry. “It’s all about geometry”, they say. The team from AM-FLOW virtualizes all material properties (plastics, colours, metallic powders), which are accessible through a digital library in order to ensure operators a “suggest rate of more than 90%” during the manufacturing process.
“We are able to deal with all the different geometries and at high speed. Moreover, thanks to artificial intelligence and machine learning, our technology will continuously improve over time. For us, the battle to upscale AM is a battle against the infinity of geometry”, Zwikker outlines.
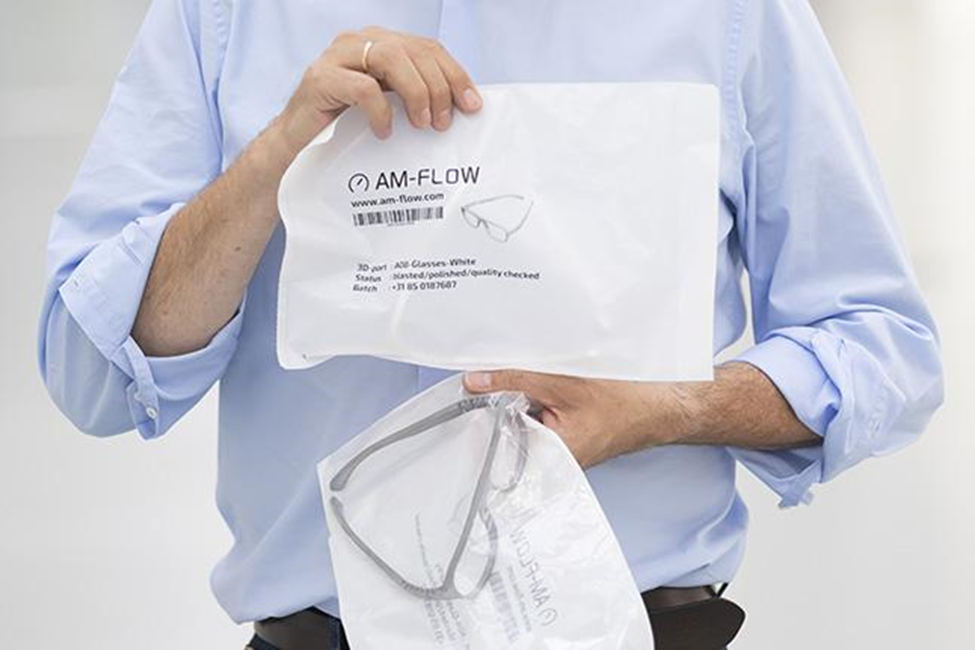
Competing with traditional manufacturing processes
It is one thing to develop a magic technology; it’s another one to make it profitable. In the socio-economic environment of the manufacturing industry, the gap between a new technology’s development and its real adoption by industries is even wider because undisputed traditions ultimately lead operators to act traditionally, forgoing the benefits of change.
This way of thinking has severely affected the integration of AM technologies to the extent that the cost per part of 3D printed parts should be lower than the cost of the same part produced via conventional manufacturing processes. For AM-FLOW’s experts, to remain competitive on the market, companies should keep in mind four parts of the iceberg: machine depreciation, material price per part, indirect costs per part and labour costs.
Our two experts highlight a number of interesting points that we have previously discussed in one of our features (3D ADEPT Mag, March-April Issue 2020 pp – 6-10). Before investing into a new additive manufacturing system, companies have several points to assess to make sure their investment will pay off: in addition to the cost of new machines, factories should take into account the material price per part.
For AM-FLOW’s CEO, the “the price of basic materials for AM remain high. If you look at what a component is costing, and what you would pay for the material, the price is still high.” Furthermore, this investment will also depend on the number of parts you will produce per batch. “Things are not the same if you invest for the production of 10 or 100 parts. The more there are parts, the more price will drop”, the CEO states. “Moreover, manual labour costs outweigh machine depreciation and raw material costs. Let’s take the example of sorting. If you just have one part to sort, that’s fine, but if there are many, it becomes complicated. That’s where automation comes into play.”
Zwikker is going even further by laying emphasis on quality: “We have been able to address challenges related to volume manufacturing. We should not forget that what people ultimately want is quality. They want to achieve quality and repeatable processes. And quality has many faces. Dealing with quality can be tricky as it
necessarily implies parts certification. That will be our next step and it will be a big change.”
Concluding thoughts
From the very beginning of this article, we told you a few companies are willing to fill the gap between the way operators “traditionally” use AM and the way the current market requires them to truly take advantage of it. To me, utilizing AM by just making any shapes that can’t be matched by machining is an old way of thinking. That was one of the first challenges of AM and we can fairly say the technology has proved out its capabilities. Today, the perfect additive production environment is centred around materials assessment, a deep understanding of tool behaviour, software programming, and a range of post-processing equipment. What factories have been waiting for, are AM technologies providers that have understood these fundamentals and AM-FLOW is likely to be one of them.