Automation solutions, from robots to software, can minimise touch labour, save costs, and improve consistency and quality. But where are we today in terms of automation in additive manufacturing? The article highlights four key trends driving the development of automation solutions in AM.
3. Automating post-production processes
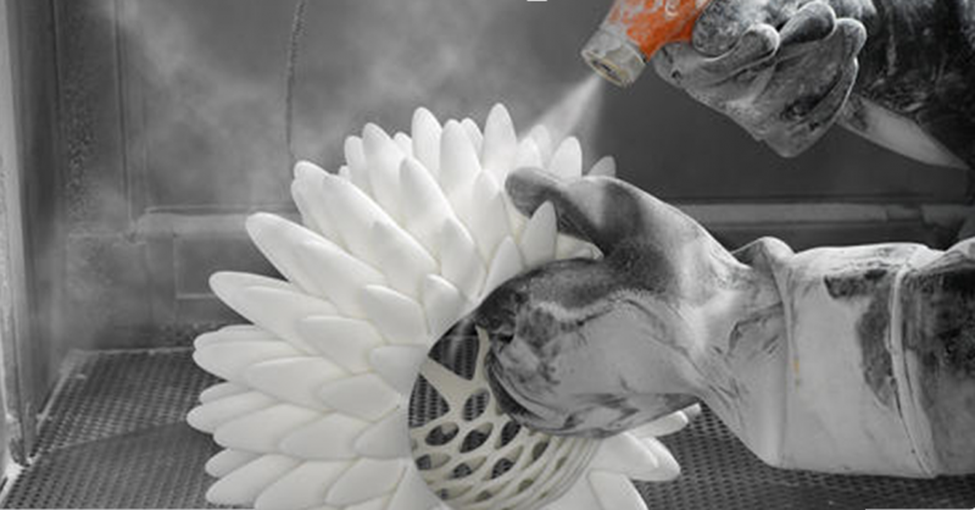
It’s estimated that 46% of businesses’ AM costs are associated with post-processing, according to the PostProcess’ 2nd Annual Post-Printing Trends Report.
Regardless of whether it is a prototype, piece of tooling or an end-use product, most AM parts require some level of post-processing. This may be as simple as removing support material, but can also include sorting, dying, polishing, as well as other processes, before the final product is ready for use. Most of the post-processing tasks are almost entirely reliant on manual labour.
Thanks to recent advances in machine learning and post-processing hardware and software, it is now possible to automate almost every part of AM post-processing, reducing labour costs and significantly improving process efficiency.
New systems are entering the market that allow parts to be extracted from a 3D printer’s build platform automatically and then moved with the help of guided vehicles to the next post-processing station.
A number of AM machine providers have also committed to automation at one level or another. EOS, for example, has developed a Shared Modules concept that integrates equipping, unpacking, transporting and sieving stages of the AM workflow, by combining different modules, transport systems and a control centre software.
Looking to automate the binder jetting process, metal binder jetting specialist, ExOne, has also released a concept of its new X1D1 automated guided vehicle (AGV), designed to enable efficient transport of build boxes.
What’s also exciting is the growing use of multi-axis robotic systems that carry parts from the 3D printers to the powder sieving, cleaning and finishing stations.
Hardware company Renishaw has showcased how the use of robots can automate one of the most time-consuming processes in metal AM – support removal. The company partnered with a start-up, Additive Automations, which has developed a robotic system for automated support removal.
Early results showed that robotic automation of support removal could reduce the average cost per part by a whopping 25%. The robots used in this process have integrated force sensors, which collect data to determine the geometry of AM parts.
The software then analyses the data, using digital twin technology. The output is then used to determine where the support structures are so that they can be removed using an end-effector tool.
Furthermore, some companies, like AM-Flow, specialise in modular solutions that offer quick and automated AM part identification, along with sorting, picking, bagging and transportation. Going forward, AM Flow wants to develop automated ID tagging, which will pave the way for full track and trace capability for AM parts across an end-to-end digitalised workflow.
Automating post-processing in AM completely changes the economics when scaling up the use of technology. It enables much higher flexibility in the factory layout and makes it feasible for manufacturers to adopt this technology for digital, rapid production.